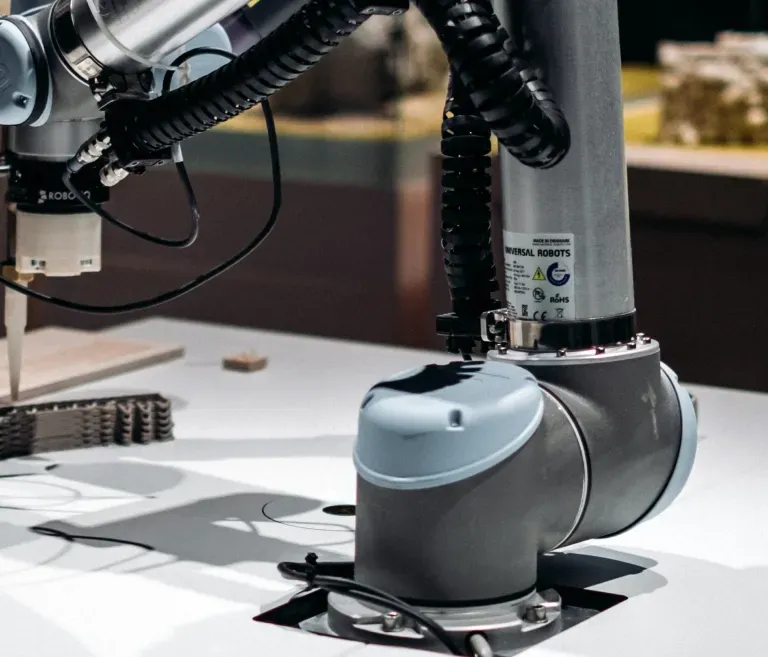
Las nuevas tecnologías al servicio de la industria
Autor: Enrique Rodal. Periodista especializado en nuevas tecnologías. Autor del libro 'Industria 4.0: conceptos, tecnologías habilitadoras y retos'
El reto de la transformación digital en las empresas e industrias de España es enorme. Según estudios como 'Smart Industry 4.0', realizado por la Consultora NTT DATA junto con el Observatorio Industria 4.0 y la colaboración del Club Excelencia en Gestión y CEL Logística, se evidencia un crecimiento exponencial de la digitalización en el sector industrial, así como un ligero aumento de la inversión en los planes de transformación digital. Con todo, la resistencia a la innovación y el cambio de los individuos sigue siendo el mayor obstáculo dentro de las empresas hacia la transformación digital. La falta de formación de los trabajadores aumenta considerablemente y es ya una de las grandes preocupaciones de las empresas. (https://clubexcelencia.org/conocimiento/plataforma-de-conocimiento/estu…) Según concluye dicho estudio, “a nivel de corporación es importante centrar esfuerzos en la formación y capacitación de los profesionales en nuevas tecnologías, metodologías, etc., que el mercado vaya demandando, de manera que nuestros profesionales sean capaces de cambiar de una herramienta a otra de manera ágil propiciando una rápida adaptación que genere mejoras en los procesos de la forma más cercana en el tiempo”. Con todo, todavía un 38% de las empresas no son capaces de identificar qué competencias son necesarias dentro de su organización en materia de Industria 4.0.
Otros estudios (http://marketing.eae.es/prensa/EAEIndustria40.pdf) revelan que el 68% de las compañías industriales españolas tienen pendiente su digitalización. De ellas, un 21% consideran que no tienen habilidades digitales en sus empresas y un 47% están inmersas en el proceso. Queda, por tanto, un largo camino que recorrer para la mayor parte de las organizaciones de nuestro país.
Está claro que existen dos velocidades bien distintas en cuanto a transformación digital e implementación de soluciones tecnológicas en las empresas. Por una parte, podemos hablar de las grandes entidades y compañías tractoras cuyo nivel de digitalización es muy elevado y poseen recursos económicos y de conocimiento para desarrollar soluciones vinculadas con tecnologías habilitadoras de Industria 4.0 (analítica avanzada de datos, inteligencia artificial, fabricación aditiva, IoT, edge computing, automatización, robótica colaborativa, sistemas ciber-físicos, fabricación flexible,....). Estas firmas invierten en I+D+ i y están pilotando proyectos vinculados con las tecnologías más novedosas.
En el otro extremo se colocan las pymes y las empresas de menor tamaño en cuanto a personal, conocimiento y recursos económicos. Hablaríamos de más del 99,8 por ciento de las firmas de nuestro país (https://industria.gob.es/es-es/Servicios/MarcoEstrategicoPYME/Marco%20E…), que son conscientes de la importancia de dar pasos hacia la transformación digital, que saben que las nuevas tecnologías les pueden ayudar a mejorar sus procesos, pero que no tienen los recursos suficientes para implementar este tipo de soluciones.
Hoy en día, hablar de Industria 4.0 es algo más que mencionar los beneficios y ahorros económicos que puede suponer para una compañía rodearse de tecnologías para mejorar sus procesos de producción. Podríamos mencionar las capacidades de la analítica avanzada de datos (big data) y la inteligencia artificial para conocer mejor a los clientes. Analizando su historial de compras, fechas en que ha comprado, qué tipo de productos ha adquirido, qué cantidades y cuál ha sido su grado de satisfacción, es factible realizar ofertas más personalizada, establecer promociones u ofrecer servicios añadidos que pueden ser de su interés. Es más, gracias a esos datos históricos de compras, tipos de productos y fechas, es posible prever la demanda en un momento determinado para adecuar los stocks o habilitar rutas logísticas para el transporte de los bienes. Conocer mejor a los clientes aporta un gran potencial de negocio.
La servitización
Si además de a los clientes, es posible conocer mejor los productos que vendemos y el uso que le dan, quizás podremos ofrecerles nuevos servicios de valor añadido. Es el concepto de servitización íntimamente ligado a la captación y el análisis de datos. Un ejemplo es el de las máquinas que recogen datos sobre su funcionamiento en tiempo real y los envían al fabricante de dichas máquinas a través de internet. Si se detecta una variación en parámetros críticos como la temperatura, las vibraciones, el número de ciclos o la humedad, el fabricante puede lanzar una alerta a su cliente, recomendando realizar un mantenimiento y anticipándose a posibles averías y paradas no programadas. De nuevo, la captación de datos y su análisis con algoritmos de inteligencia artificial son fundamentales. Ya no se trata de vender una máquina, sino de ofrecer un conjunto de servicios añadidos que dan valor a esa máquina y que conllevan un nuevo estadio de relación con los clientes.
Otro factor que se sustenta en las nuevas tecnologías es la Fabricación Cero Defectos. Está claro que las industrias de nuestro país quizás no pueden competir en precios con empresas de otros lugares más lejanos, pero sí que pueden competir en cuanto a calidad. Se trata de supervisar lo que ocurre durante todo el proceso productivo: desde la fase de diseño, fundición, forja, fabricación y montaje. Hay que revisar todo desde el principio, porque si algo está mal en las primeras fases de producción terminará afectando a las últimas. Si hemos cometido fallos en el diseño, tendrá su efecto. Si algo se ha hecho mal durante la fundición, forja o montaje de una pieza, tendrá sus consecuencias. Disponer de sistemas y herramientas tecnológicas que permitan fabricar con mayor calidad es un valor añadido. Al ser capaces de supervisar la calidad de un simple tornillo o tuerca antes de montarlo en, por ejemplo, un motor, evitaremos muchos problemas y sabremos que la vida útil de ese motor estará ajustada a los parámetros establecidos por el fabricante. Los sensores avanzados capaces de medir múltiples parámetros físico-químicos en tiempo real, la visión artificial, la tomografía o las diferentes herramientas que se emplean en metrología son los aliados perfectos para detectar fallos.
A la hora de hablar de calidad, no solo sirve con mencionarla, sino que hay que demostrarla. Las tecnologías DLT o tecnologías de registro distribuido, como es el caso de Blockchain, permiten almacenar los datos y la información en redes descentralizadas que no pueden ser modificadas sin el permiso de todos los miembros de esa red. Es decir, no se puede manipular la información sin el permiso de todos los participantes. De esa forma, es posible recopilar toda la información de trazabilidad del proceso de fabricación de cualquier producto y exponerla a los proveedores o clientes para garantizar que todo se ha hecho en base a las especificaciones predefinidas.
Las empresas aspiran a fabricar productos de mayor calidad, aunque sean más caros. Y otra aspiración es a producir bienes personalizados. El concepto de customización masiva, también ligado a la Industria 4.0, consiste en implementar soluciones tecnológicas que permitan personalizar un producto en base a las necesidades de los clientes. Podemos hablar del uso de robots colaborativos para una fabricación flexible o de emplear tecnologías de fabricación aditiva para crear bienes únicos. Los ejemplos son múltiples: desde un salpicadero de coche personalizado con el nombre del dueño, pasando por envases de alimentos en los que el cliente selecciona la proporción de productos que lleva, hasta un ordenador con una configuración concreta y ajustada a ciertas necesidades.
Sostenibilidad y eficiencia energética
Hablar de sostenibilidad y eficiencia energética ya era clave hace unos años cuando desde la Asamblea General de las Naciones Unidas se impulsó la Agenda 2030 para el Desarrollo Sostenible y sus 17 Objetivos de Desarrollo Sostenible (ODS). (https://sdgs.un.org/2030agenda) Siete años después de la firma de este acuerdo, la crisis energética provocada por la Guerra de Ucrania pone más en evidencia, si cabe, la necesidad de impulsar acciones para reducir el consumo energético. En este sentido, adquieren gran relevancia las herramientas tecnológicas orientadas a la medición de consumos energéticos y ofrecer pautas y consejos para una mayor eficiencia energética. Los smart grids o contadores inteligentes que registran toda la información de consumo energético y la analizan con algoritmos de inteligencia artificial, son soluciones cada vez más empleadas en el mundo industrial. En este caso, se conjugan la eficiencia energética y el ahorro económico, dos aspectos a cada cual más relevante.
Otras soluciones tecnológicas vinculadas con la sostenibilidad en la industria se orientan a reducir el gasto en iluminación de las empresas mediante la instalación de sensores de luz que adecúan la intensidad a las condiciones de iluminación, el uso de sensores de temperatura, humedad o calidad del aire que permiten adaptar la temperatura de una estancia, o la generación local de fuentes de energía renovables mediante la instalación de paneles solares para captar energía fotovoltaica o termosolar. Todo ello sin olvidar los retos que supone la logística y las posibilidades que ofrece la inteligencia artificial para optimizar rutas de transporte de cara a minimizar el uso de combustibles fósiles.
Pero más allá del ahorro en costes económicos, optimizar los recursos, fabricar productos de mayor calidad, personalizar nuestra producción o ser más eficientes, una aportación de las nuevas tecnologías a la industria se centra en su uso para la prevención de riesgos laborales y accidentes de trabajo. Existen tecnologías como los drones o los vehículos autónomos capaces de realizar tareas arriesgadas que hasta ahora eran llevadas a cabo por personal humano. Se han desarrollado un sinfín de sensores capaces de detectar fuego, humo o la existencia de gases nocivos y que alertan en caso de riesgo. Se extiende el uso de exoesqueletos que ayudan al personal a realizar ciertas tareas físicas gravosas. Tecnologías como la visión artificial permiten analizar el comportamiento de las personas y advertir en caso de riesgos, como un desmallo o sufrir una caída en entornos peligrosos. El impacto de prevenir un accidente y salvar una vida, no se puede cuantificar económicamente de ninguna manera.
Y hablando de empleados y seguridad, las nuevas tecnologías también ayudan en todo lo que tienen que ver con su formación. Se han desarrollado simuladores que permiten practicar el manejo, por ejemplo, de una carretilla elevadora, sin que exista ningún riesgo físico. También se realizan simulaciones mediante técnicas de realidad virtual para llevar a cabo simulacros de planes de emergencias. Las tecnologías inmersivas facultan recrear células de fabricación en las que los operarios pueden entrenar cómo se manejan ciertas máquinas, sin riesgo para la integridad de dichas máquinas y sin costes añadidos de consumo energético o de uso de bienes de producción. Sin olvidar otras tecnologías que permitirán a las empresas formar de una manera más eficaz e interactiva a sus trabajadores, supervisando en todo momento cuáles son sus conocimientos y qué tipo de habilidades es necesario reforzar.
El futuro
Las nuevas tecnologías han llegado al mundo industrial para quedarse. Después de hablar durante muchos años de Industria 4.0, ahora ha llegado el momento de ir un paso más adelante hacia la Industria 5.0. El futuro de las nuevas tecnologías aplicadas a la industria pasa por la digitalización y la captación masiva de datos, la aplicación de inteligencia artificial para analizar esos datos, la utilización de herramientas de visión artificial y Procesamiento del Lenguaje Natural para el aprendizaje de máquinas, la recreación de espacios reales y virtuales (metaverso) y el uso masivo de hardware cuántico que admitirá analizar millones de datos en tiempo real y resolver problemas de cálculo que los sistemas de computación actuales no pueden solventar. Todo ello sin olvidar la conectividad inalámbrica, como el 6G, que permitirá el envío masivo de datos con una baja latencia.
Mirando al futuro, según un informe de Accenture, la inteligencia artificial podría llegar a duplicar las tasas anuales de crecimiento económico en todo el mundo en 2035, cambiando la naturaleza del trabajo y estableciendo una nueva relación entre el hombre y la máquina. El impacto de la inteligencia artificial en los negocios aumentará la productividad del trabajo hasta en un 40%. Según este mismo estudio, en España la IA permitirá pasar en 2035 de una tasa de crecimiento anual del 1,7% del PIB a una cercana al 2,5% (https://newsroom.accenture.com/news/accenture-report-artificial-intelli…).
En lo que se refiere al metaverso, un estudio de la consultora McKinsey estima que para el año 2030 alcanzará un valor de 5.000 billones de dólares. El mismo informe calcula que los usuarios pasarán unas 6 horas al día inmersos en el metaverso (https://www.mckinsey.com/capabilities/growth-marketing-and-sales/our-in…). Las previsiones referidas a la computación cuántica observan que el gasto mundial en esta tecnología alcanzará los 7.600 millones de euros en 2027, después de registrar un crecimiento anual medio del 50,9% en los próximos seis años (https://www.idc.com/getdoc.jsp?containerId=prUS48414121).
Son datos que revelan que estas tecnologías van a dominar el futuro a corto plazo. La inteligencia artificial ya está aquí, la computación cuántica cada vez es más tangible y el metaverso es más un deseo que una realidad, pero despierta el interés de las principales compañías del mundo, lo que es casi una garantía de éxito.
La Industria 4.0 y el desarrollo de soluciones basadas en estas tecnologías es un reto al que todas las empresas estarán obligadas a sumarse muy pronto si quieren seguir subsistiendo en un contexto de competencia global.